Elon Musk just announced he plans to counter cheaper competition from China with a $25,000 electric car. To get there, he wants to completely overhaul the century-old manufacturing logic pioneered by Henry Ford, where the car moves along an assembly line.
Instead, he's envisioning an unboxed approach that would assemble parts simultaneously in dedicated areas, reducing manufacturing footprints by over 40%. This change could cut production costs in half, which is crucial for reaching the $25K price point (and boosting its stock price, which plummeted by 28% this year).
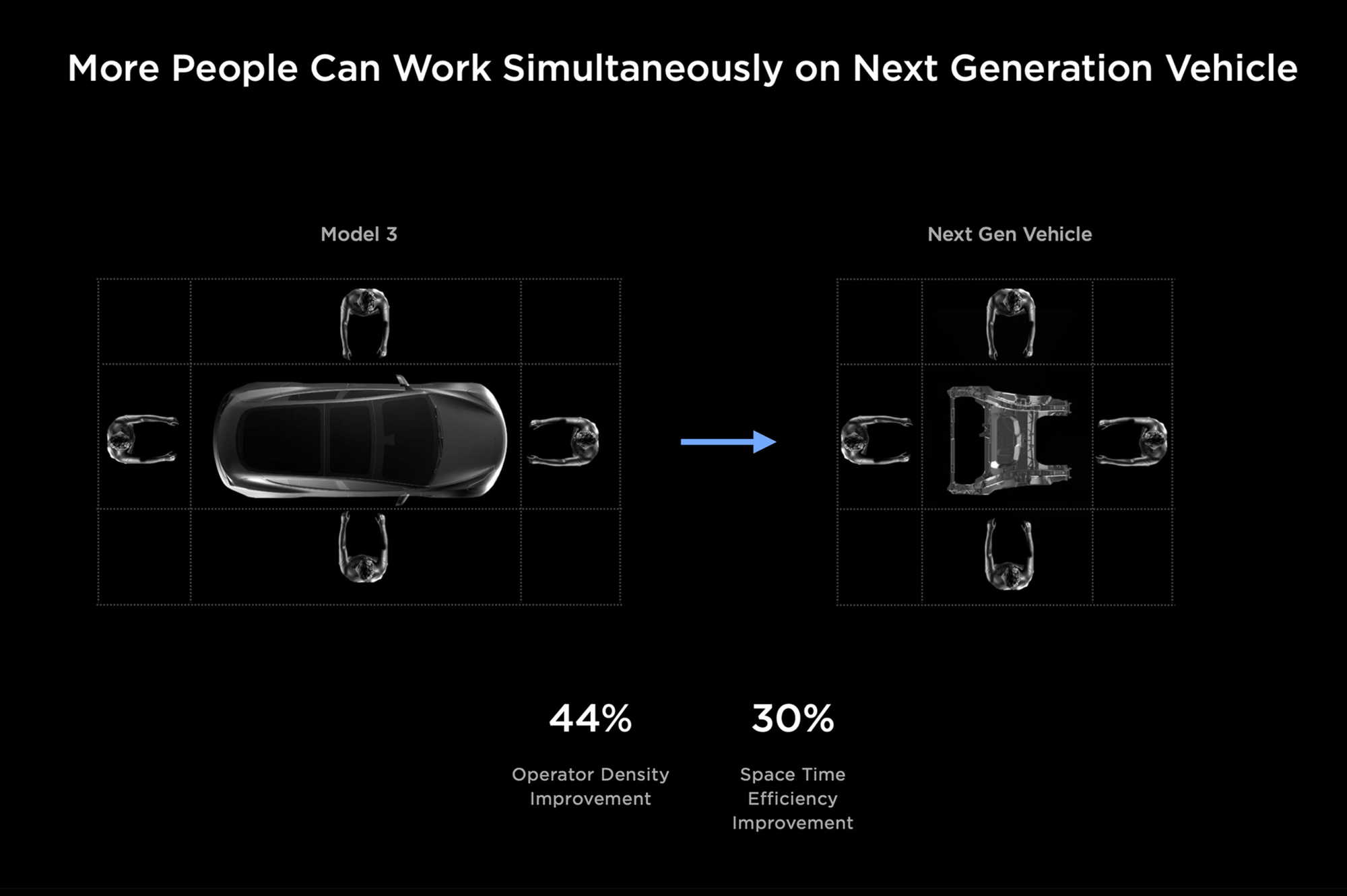
However, Musk being Musk, details on progress remain scarce, raising skepticism among investors. Nonetheless, we should pay attention. One of the key successes of Tesa has been reinventing from the ground up how car manufacturing worked when they started being serious about delivering their first cars. They were nearly bankrupt because of that at the time!
Meanwhile, Hyundai seems to be further ahead, showcasing his Singapore 'factory of the future' working around the same idea. Smaller factory footprint, much more reassembling, and flexible robotization.
The keyword here is cell manufacturing.
The change in factory footprint is indeed quite revolutionary, maybe speaking of a future where micro-factories could be spread out all over a region to provide on-demand manufacturing and deliveries:
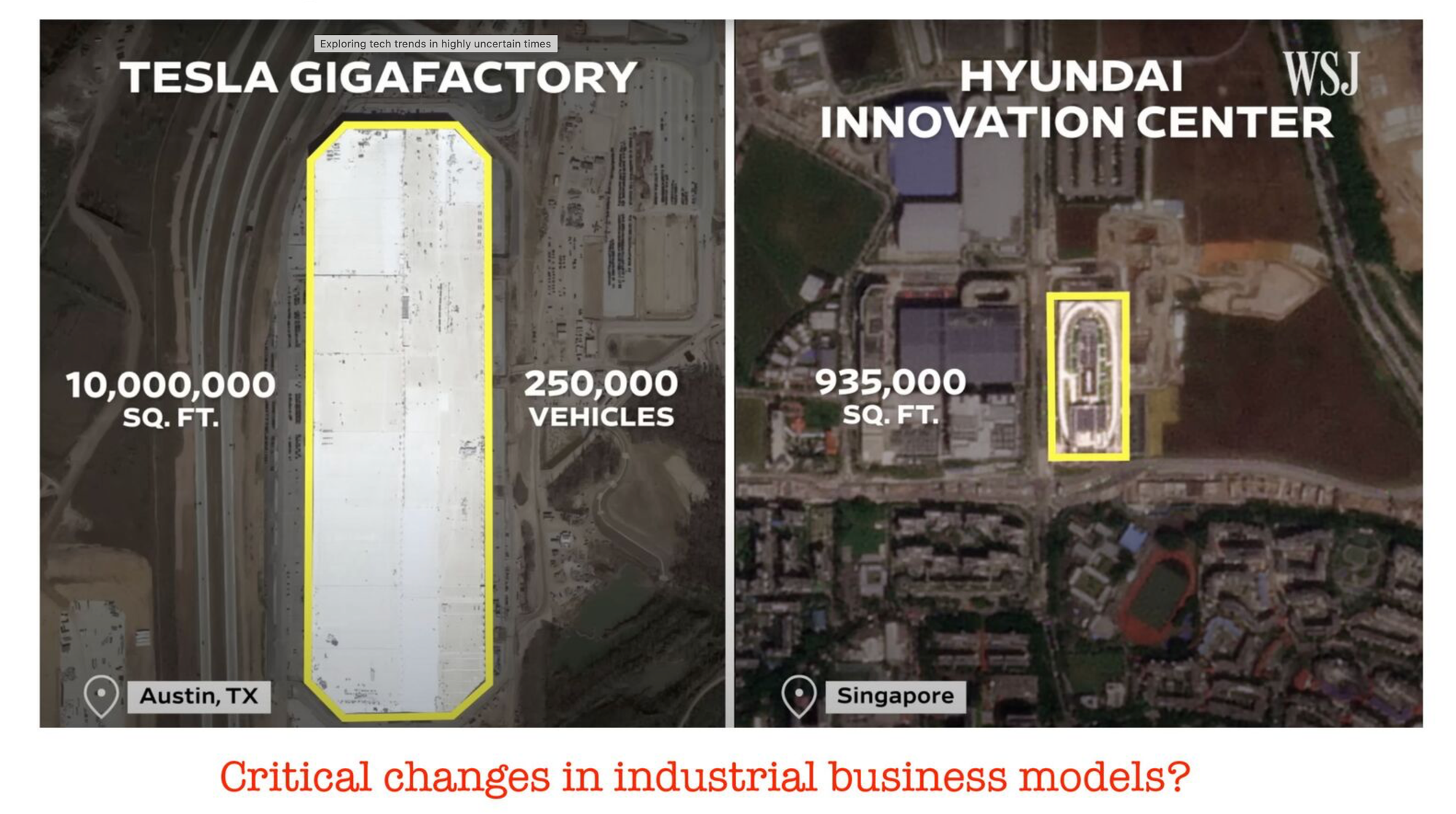
In all this, remember that Nvidia will play a central role in providing the tools to redesign and reimplant all these new factories... And, as an added hint, I'd recommend you relearn the term 'Glocal' (a strategy where products are designed and branded from a global standpoint but sourced, produced, and sometimes adapted locally.)